Thanks Jon, I agree. Some things just can’t be sorted out at a distance. It’s back to IGFS and HPR Baryta for me.
A belated postscript to this issue. I’ve again printed on EEF / TPP the image of that young jazz pianist that featured in posts #14 & #49. This time I got no mottling. There was a little “texture” in some areas before GO, but after GO of 30K it was just fine, as Jeff saw on Monday when he passed through. Some surface texture, as was discussed in another thread in relation to Cone5, but no mottling.
So what has changed? This is the exact same printer, paper batch and inks, other than shade 1. Well, my previous attempts were with WN1 and now I’m using SEL1, but Jeff was / is using SEL1, so that’s unlikely to be the cause on its own. I guess some batch variation is theoretically possible but unlikely.
The other change is that I’m now using P2 rather than K7, so the curves are different. You’re recall that I successfully remapped the x880 P2 curves to the R1900, and that’s what I used. There are inkset-specific P2 curves, and this was the one for SE. On this occasion I relinearised the curve using Roy’s droplet, although the standard curve was already fairly good.
This time the average density of the 100 patch in the 21x4 was only around 1.98, whereas with the standard R1900 K7 curve it was 2.13. My view is that the mottling was occurring because the black ink limit for some of those K7 EEF curves was set a bit high, and whether there was mottling or not varied with the specific printer, paper batch, humidity and phase of the moon. I.e. there wasn’t enough latitude to allow for any variation. More dMax on gloss is better, but perhaps some papers need not to be pushed too far, in order to allow for such variations.
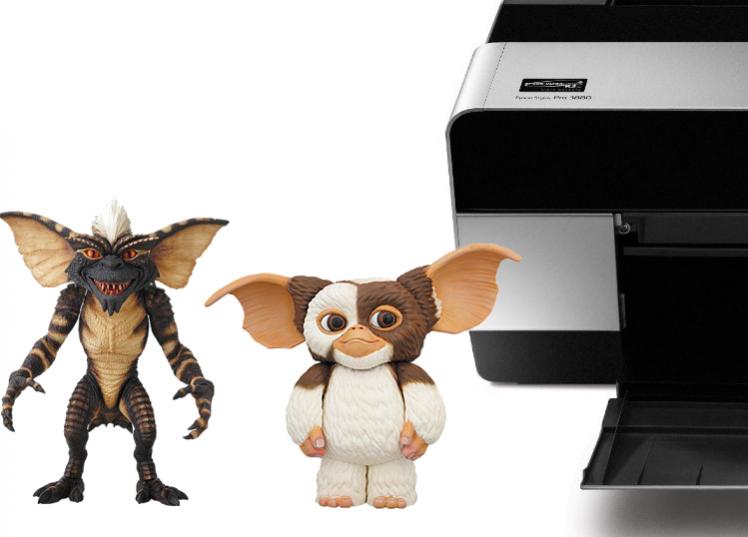
you never know…
I can tell that’s an Epson Pro printer in that photo, mostly likely a 3880, and we all know that Epson Pro printers don’t have gremlins. So I have grave fears that that image has been Photoshop-ed. As a photojournalist, you could get into a lot of trouble for that. Lose all your Pulitzer prizes and so on.
More seriously, … You recommended EEF. However the mottling on it has been a pain for some of us. We have done testing and Dana has done testing and other users have also had issues. I’ve made an interesting discovery, which I thought may be of relevance. I don’t think it’s just Gremlins that there’s no mottling with a P2 / K6 curve that just so happens to deliver a lower dmax at 100.
Hopefully this is the last post on this. There has been a little more testing by Jeff and I. The test image of that young jazz pianist was printed on EEF using a three printers and a mix of curves.
As previously reported, there was mottling if it was printed on Jeff’s 3880 using the K7 curve. There was mottling on my R1900 using the K7 curve.
We’ve printed the image again using P2 curves. Jeff printed it on his 3880 (before decommissioning it) using the P2 Neutral curve (remapped so that PK came from the K channel and not Yellow). He also printed it on his new R2000 using the same curve remapped to the R2000. As per post #52, I printed it on my R1900 using the remapped P2 Special Edition curve. There was no mottling in any of these P2 prints.
I still think that the black limit was too set too high on the earlier K7 curves. I may have worked on some printers, but was too close to the edge to allow for any variability in printers, humidity, paper batches, phases of the moon. It seems about right in these later P2 curves.
I do want to jump in here and say that the EEF in the USA has changed since we made our last bulk sheet purchases in 2013 and developed QTR curves for it. When we like a sheet, we buy a LOT of paper for Cone Editions. We do this to avoid changes in our production. We have always done this practice - even since the days of the 1980s when were a photogravure studio. Paper is always the bane of our existence as printmakers. We still have 100s of sheets of 24x30 EEF that we now realize are precious beyond precious. The new EEF is not a sheet that we would consider purchasing or offering at this point. It’s too ordinary.
We only just noticed this recently because we are re-upping on smaller sizes which were shipped to us in black boxes. Our supplier said this change happened beginning of 2014. We can still source original EEF in rolls, but not in sheets. It’s devastating because I actually use this paper myself as well as offer it to our clients.
The new EEF packaged in black boxes has no relationship whatsoever to the EEF we purchased for many many many many years that came in white boxes. The James Nachtwey prints at the Currier Museum of Art that are currently on exhibition are Selenium inks on the original EEF. If James saw the current EEF - he would have refused it.
What are the differences we observe?
The original EEF is very bright white.
[I] The new EEF is warmish near the red side of white.
[/I] The original EEF was thicker in “hand”.
[I] The new EEF feels thinner in “hand”.
[/I] The original EEF had a surface texture somewhat like Ilford fiber based silver papers - just barely rolling texture.
[I] The new EEF has a typical surface like cheaper baryta papers - nondescript.
[/I] The original EEF could take a good ink load.
[I] The new EEF can not take much ink load.
[/I] The original EEF was a house paper for Cone Editions to accompany the warmer Type 5.
The new EEF is really not worth stocking as an option for our clients.
We are now making new curves for the new EEF. And the black limit will have to be much lower… It is rather ordinary as a sheet…and we’re a bit heart-broken to lose such a great sheet. It really is night and day when you put one sheet on top of the other or side by side…it is so obvious.
So it wasn’t quite the last post. A couple of follow-up questions.
-
Which version of EEF were the current P2 curves made on? The lower ink loading suggests that they were made on the newer version, but the dates on them are mostly Nov 2012 to Feb 2013, making it likely that they were made on the older version. Which is a little confusing.
-
Jeff shipped a couple of sheets of TPP to Dana for testing. Does she recall / can she confirm that these were the newer version? You’d think so, given the problems we had, although her test results with that paper back in post #45 suggested that it wasn’t the cause of our mottling problems. Which is also a little confusing.
[QUOTE=Brian_S;9218]So it wasn’t quite the last post. A couple of follow-up questions.
-
Which version of EEF were the current P2 curves made on? The lower ink loading suggests that they were made on the newer version, but the dates on them are mostly Nov 2012 to Feb 2013, making it likely that they were made on the older version. Which is a little confusing.
-
Jeff shipped a couple of sheets of TPP to Dana for testing. Does she recall / can she confirm that these were the newer version? You’d think so, given the problems we had, although her test results with that paper back in post #45 suggested that it wasn’t the cause of our mottling problems. Which is also a little confusing.[/QUOTE]
-
Official release (not customer customs) for EEF are on pre-2014 inventory and therefore prior to the introduction of a new media under the same name. The ink load was lowered for a different reason than the media itself.
-
I don’t think we considered TPP to be EEF based upon your experience with it and that it had a different name. I will have to revisit the TPP and compare it to the new EEF to see if its the same - or if it is a total different beast. I will report back.
Which just goes to prove why I have always been highly suspicious of paper from printer manufacturers. We have all spent a lot of time and money on this only to find out that we were comparing apple to oranges. Thanks a lot Epson.
Now it turns out that your Apples and our Apples are the same. The TTP Jeff sent us looks and prints like the old EEF.
We need agent Mulder…
So we should buy up all we can while we can?
Mould-made fine art paper from Europe is and has always been very seasonal. These are papers that are formed in traditional papermaking equipment using cotton rag and linters and almost always local spring water. The mills are almost always situated by the water source which is how they came to be in the first place. So Winter made paper is different than Summer made paper, etc. The quality of the water changes dramatically in the spring during the melts, and in the winter when its clearest, etc… And this has an effect on the formation of the sheet. It is relevant. The papers are coated for inkjet (usually at a different facility). This coating changes frequently due to raw ingredients… So paper is more changeable than inks.
When you find a sheet (batch#) that you really really like - it is wise to buy a supply of it. It stabilizes a studio, or a series of work, or possible an effect that can not be duplicated, etc … In our case, Cone Editions is printing for clients who store their images with us and request reprints. So we often buy enough paper to last years - so that we do not need to reproof. Because we are manufacturing our own inks - we have stabilized that portion which we would not have control over if using OEM inks (which change occasionally). So we try and stabilize our output as much as we can for as long as we can. Reproofing is time consuming and expensive. For every print on demand project we keep a match print (signed BAT proof).
This is and how it always has been in inkjet printing since the early days of the IRIS 3047. In the early 1990s, studios began trading paper batches and hoarding certain batches of Somerset Velvet uncoated. There was at one time, a list going around through the studios we had setup, for trading batches of paper. In those days, color management was via making neutral from CMYK rather than ICCs (which were not yet in practice). Today it is easier to make a new profile or a linearization when a paper changes dramatically. But, if the coating or the base changes so dramatically that the media itself is less desirable - then one rues the opportunity missed to hoard it. Hoarding is expensive. But - making art is expensive.
I would say that with discounts available in bulk purchasing, that it is wise to buy at least a years worth of media by batch# if you find a sheet that you really like. Chances are it will change. This may actually be easier for the occasional printmaker - than for a studio that produces 1000 sheets a month. Safe storage becomes an issue. Should be cool and dry (and no mice!)
I want to add that we liked the original Exhibition Fiber paper because of the whiteness, which is one of the main reasons we don’t like the new warm version.
Regarding mottling in shadows, the new paper is better than the old/white version (I see NO mottling with the new/warm paper). The new/warm paper looks good with GO, but is flat/not very glossy without GO (which would effect people printing with color inks without GO). Mottling is very bad on old/white ExFiber without GO, and still present but much better after printing GO (though this seems to come and go, I think depending on temp +/or humidity levels, I’ve printed on the old/white EEF without mottling over the years, though my tests today are mottling- and the current conditions are 73F and 36% H).
Here are a few scans showing the paper white and mottling differences with Traditional Photo Paper (from Jeff G, which is the same as the OLD/white Exhibition Fiber paper) and NEW/warm Exhibition Fiber Paper. NOTE: each scan is labeled at the bottom with the paper/setting:
Thanks Dana!
Thanks to both of you. This thread has been rolling along since March 22. I’ve certainly learned a lot along the way with it. That’s quite a difference between the same paper.
I echo Jeff’s thanks.
The big news for me in this is the mottling you get now with TPP when you didn’t back in post #45. Back then, we concluded that the paper wasn’t the problem. Something else must have been causing our mottling. But now it is the culprit.
What is going on with this paper (old version)? How could you (IJM) print for clients with it when you get such a variable outcome? I suppose it’s still possible that TPP and old EEF aren’t exactly the same, although I don’t see any evidence for that in any of the above.
Jeff’s initial box of A4 TPP has gone. I bought a second to try it out for colour work, and only did a few Piezo prints on it using the remapped P2 curves out of an obsessive interest to understand what might have been causing our mottling. When there was none initially using P2, we conducted as wide a range of tests as we could, reported in post #55.
I am disinclined to use a paper for Piezo when I can’t predict how it’s going to behave, and I don’t understand what is driving the differences. Given these IJM experiences, it could still emerge when using the P2 curves.
Jeff - when you’re next in at our normal supplier, perhaps you could ask them if they know of any recent changes in TPP, noting that there seems to be quite a dramatic change in US-sourced EEF.
On the subject of old EEF and new EEF, this post was interesting:
The poster runs a print studio and does a lot of printing, so speaks from some experience.
EEF certainly is their most “tweaky” paper. I stopped printing on it long ago when running labs in Chicago because of the variability issues with EEF . . . . Glad Epson is using platine as their main ef paper now.
cheers,
W
If you’re referring to Epson Legacy Platine, do you have a view on whether this is just Canson Platine rebranded, as suggested/claimed on Lula, and ditto for the other new Epson papers?
After this experience, I have abandoned all Epson papers other than EEM. Having also been told that the paper can be different from region to region, I lost all interest. I’ve always been wary of buying paper from printer manufacturers, and this is a good example of why you shouldn’t.