I’ve had a play with this paper. Jeff gave me several sheets to test. So I printed that image above (one of mine actually) of the young jazz pianist in post #8. The image probably isn’t the best demonstration of K7, with all that black (not unusual for live jazz), but it is a good test of the behaviour of deep shadows. I think Jeff sent you (Jon) the original of the image in separate correspondence.
I printed it on my R1900 using the curve for EEF that ships with QTR, so quite a different printer and a different curve to what Jeff used. I am using K7 SE with WN Opaque, so only shades 6 and 7 are the same inks as the neutral set that Jeff used. My location is quite different to Jeff’s and humidity is not as bad, although it’s been raining here recently, so it’s not all that low either. So all in all it’s quite different. GO was 30K. Print was well dried before measuring and then coating and then remeasuring.
I first did a linearity check both without and with GO, the results of which are below. It’s not as linear as one would like, but it’s not the worst I’ve seen, and definitely nothing like Jeff’s, esp in the deep shadows. The GO helps the highlights but not the shadows. The gentle, non-extreme nature of the non-linearity can be dealt with using a Photoshop curve - I have a spreadsheet that constructs such curves from the linearity plot.
Without GO

With GO:
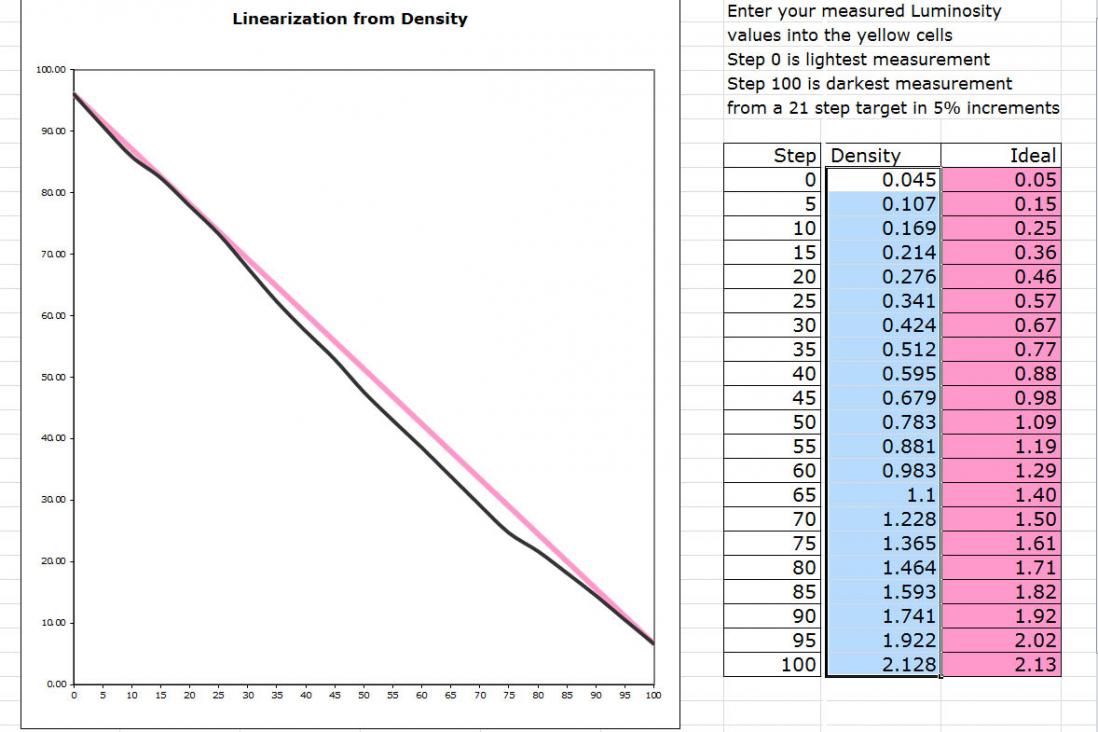
Scans of an extract of the printed image without and with GO are below. There was a fair bit of mottling in the very deep shadows in the uncoated print. The GO coating removed it some some areas completely, but in the areas where the K values in PS are 98%- 99% it’s still there to some extent. It’s not easy to see, and may be hard in the scan, but you can see in in certain types of oblique lighting.
Without GO:

With GO:

As a comparison, I printed this image on the same paper using my OEM 2880. I created an ICC profile for ABW EEF so I can roughly match the two prints. There was no mottling (or bronzing), despite the dmax being 0.4 higher, reaching 2.5 coated, compared to 2.1 coated.
My results seem to indicate that Jeff’s mottling problem won’t be eliminated by a custom curve, since my linearity is not that bad, and the problem still occurs.
Based on our experiences, it’s not a paper that I’d recommend for K7, although the K3 ABW print looks just fine.
p.s. Looking at the coated print again, something is odd. Just how visible the mottling is depends on the light and the angle. But more than that, in the areas that had clear mottling pre-GO, there’s a marked difference to the rest of the print post-GO. I.e. The rest of the print looks nicely glossy. But the real black areas - 98% K and higher - are not glossy at all - they look almost matte with some faint mottling. Why is this, since they’ve had a coating of GO too? This mixture of matte and gloss looks odd, and the matte-looking areas are quite different to the bronzing you get on most glossy papers before the GO coating.